Descubre todo sobre los sensores de presión y cómo funcionan
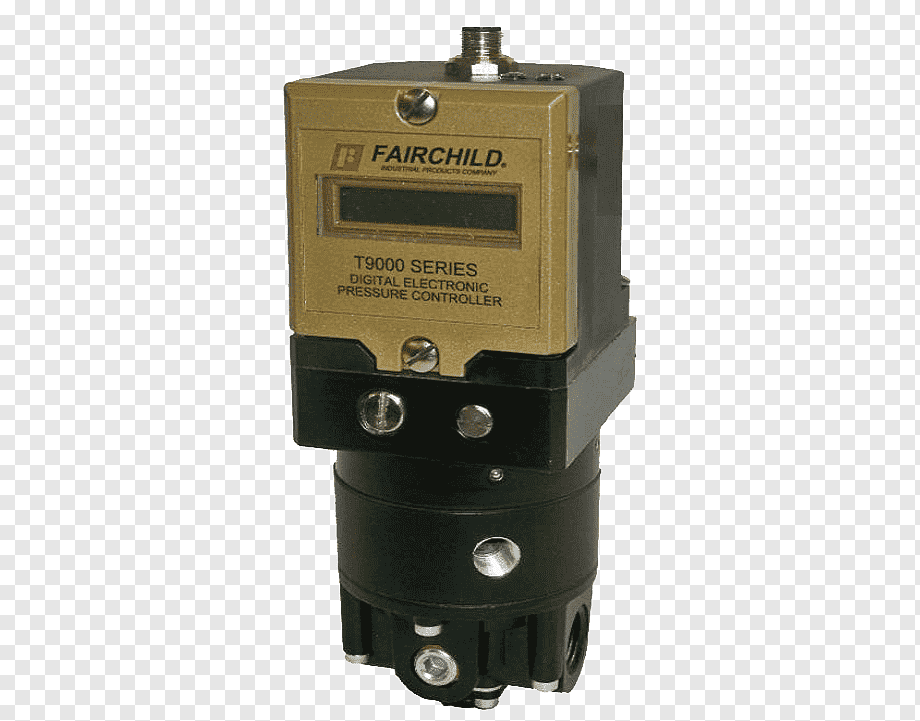
Los sensores de presión son dispositivos que se utilizan ampliamente en diversas aplicaciones, desde la industria automotriz y aeroespacial hasta la medicina y la robótica. Estos sensores permiten medir la fuerza ejercida sobre una superficie o un fluido, proporcionando información crucial para el control y monitoreo de procesos y sistemas.
Vamos a adentrarnos en el mundo de los sensores de presión, explorando cómo funcionan y cuáles son las diferentes tecnologías utilizadas en su diseño. Además, veremos algunas de las aplicaciones más comunes de estos sensores y los desafíos técnicos que enfrentan. ¡Prepárate para descubrir cómo estos pequeños dispositivos hacen grandes cosas!
- Cuál es la definición de un sensor de presión
- Cómo funciona un sensor de presión
- Cuáles son los diferentes tipos de sensores de presión disponibles en el mercado
- Cuáles son las aplicaciones comunes de los sensores de presión
- Qué características debes considerar al elegir un sensor de presión
- Cómo se calibra un sensor de presión y por qué es importante
- Cuáles son los beneficios de utilizar sensores de presión en diversas industrias
- Cuáles son las principales diferencias entre un sensor de presión absoluto y uno diferencial
- Cómo se instalan y mantienen los sensores de presión correctamente
- Cuáles son las limitaciones y desafíos asociados con el uso de sensores de presión
- Qué avances tecnológicos se han realizado en el campo de los sensores de presión en los últimos años
- Espero que estos temas te sean útiles para escribir tu artículo. ¡Buena suerte!
Cuál es la definición de un sensor de presión
Un sensor de presión es un dispositivo electrónico que se utiliza para medir y registrar la presión de un fluido o gas en tiempo real. Estos sensores son ampliamente utilizados en una variedad de aplicaciones industriales, automáticas y médicas, ya que proporcionan información crucial sobre la presión en diversas situaciones.
Existen diferentes tipos de sensores de presión, pero en general, funcionan mediante la conversión de la presión en un cambio detectable en alguna propiedad física. Esto puede ser el cambio en la resistencia eléctrica, la capacidad, la frecuencia o la fuerza aplicada a través de una membrana.
A medida que la presión aumenta o disminuye, el sensor cambia su propiedad física correspondiente y este cambio se convierte en una señal eléctrica o mecánica. Posteriormente, esta señal se procesa y se interpreta mediante circuitos electrónicos para obtener una lectura precisa de la presión.
Los sensores de presión suelen estar equipados con una parte sensible, conocida como elemento primario, que interactúa directamente con el fluido o gas cuya presión se está midiendo. Dependiendo del tipo de sensor, el elemento primario puede ser un diafragma, un tubo capilar, una celda de carga o un transductor de silicio, entre otros.
Además, los sensores de presión pueden clasificarse en dos categorías principales: absolutos y relativos. Los sensores de presión absoluta miden la presión en relación con el vacío absoluto, mientras que los sensores de presión relativa miden la presión en relación con la presión atmosférica.
Cómo funciona un sensor de presión
Un sensor de presión es un dispositivo que se utiliza para medir y monitorear la presión en diferentes sistemas. Estos sensores son ampliamente utilizados en una variedad de industrias, desde la automotriz hasta la aeroespacial, pasando por la manufactura y la medicina.
La función principal de un sensor de presión es convertir la presión aplicada en una señal eléctrica que pueda ser medida y analizada. Esto permite obtener información precisa sobre la presión en tiempo real y tomar decisiones basadas en estos datos.
Hay varios principios de funcionamiento utilizados en los sensores de presión, pero uno de los más comunes es el principio de deformación elástica. Este principio se basa en la idea de que cuando se aplica presión sobre un material elástico, como un metal o un polímero, este se deforma en proporción a la presión aplicada.
En un sensor de presión basado en el principio de deformación elástica, se utiliza un elemento sensible al cambio de forma, como una membrana o un diafragma, que se flexiona cuando se aplica presión. Este elemento está conectado a una celda de carga o a un transductor, que convierte la deformación mecánica en una señal eléctrica proporcional a la presión aplicada.
El transductor utilizado en un sensor de presión puede ser resistivo, capacitivo o piezoeléctrico, dependiendo del principio de operación específico. Por ejemplo, en un sensor resistivo, la deformación del material elástico cambia la resistencia eléctrica, lo que se traduce en una variación de la señal eléctrica. En un sensor capacitivo, la deformación del material cambia la capacitancia, mientras que en un sensor piezoeléctrico, la deformación genera una carga eléctrica proporcional a la presión aplicada.
Una vez que se obtiene la señal eléctrica, esta se puede amplificar, filtrar y convertir en datos digitales para su procesamiento posterior. Los sensores de presión también pueden tener otros elementos adicionales, como compensación de temperatura para mejorar la precisión y estabilidad, y protección contra sobrecargas o condiciones adversas.
Un sensor de presión funciona convirtiendo la presión aplicada en una señal eléctrica proporcional para su posterior análisis y monitoreo. A través de diferentes principios de funcionamiento, estos sensores proporcionan información precisa y en tiempo real sobre la presión en diversos sistemas y aplicaciones.
Cuáles son los diferentes tipos de sensores de presión disponibles en el mercado
En el mercado actual, existen varios tipos de sensores de presión disponibles para diferentes aplicaciones. Algunos de los más comunes son:
-
Sensores de presión capacitivos
Este tipo de sensor utiliza una placa de condensador para medir cambios en la distancia entre las placas debido a la presión aplicada. La capacitancia varía proporcionalmente con la fuerza ejercida y se puede determinar mediante un circuito de medición.
-
Sensores de presión piezoeléctricos
Los sensores de presión piezoeléctricos utilizan materiales piezoeléctricos que generan una señal eléctrica cuando se les aplica presión mecánica. Estos tipos de sensores son adecuados para mediciones rápidas y de alta frecuencia.
-
Sensores de presión resistivos
Los sensores de presión resistivos utilizan una membrana delgada en la que se encuentra un puente de Wheatstone. Cuando se ejerce presión sobre la membrana, esta se deforma y cambia la resistencia del puente, lo que se traduce en una señal eléctrica proporcional a la presión aplicada.
-
Sensores de presión de membrana
Estos sensores están compuestos por una membrana flexible que se deforma cuando se le aplica presión. La deformación de la membrana se mide mediante diferentes métodos, como cambios en la capacitancia, resistencia o el desplazamiento de una varilla.
Estos son solo algunos ejemplos de los tipos de sensores de presión disponibles en el mercado. Cada uno tiene sus propias ventajas y desventajas, y es importante seleccionar el tipo adecuado para cada aplicación específica.
Cuáles son las aplicaciones comunes de los sensores de presión
Los sensores de presión son dispositivos electrónicos que permiten medir y convertir la presión en una señal eléctrica. Debido a su versatilidad y precisión, estos sensores tienen una amplia gama de aplicaciones en diferentes industrias.
A continuación, se enumeran algunas de las aplicaciones más comunes de los sensores de presión:
- Industria Automotriz: Los sensores de presión se utilizan en sistemas de control de emisiones, sistemas de inyección de combustible, sistemas de frenos ABS y para controlar la presión de los neumáticos. También se utilizan en la industria aeroespacial para el control de vuelo y en sistemas de propulsión.
- Industria Médica: En medicina, los sensores de presión juegan un papel crucial en la monitorización de la presión arterial, la ventilación mecánica, la diálisis y la detección de obstrucción de tubos de respiración. También se utilizan en la medición de la presión intraocular en oftalmología.
- Industria Alimentaria y Farmacéutica: Los sensores de presión se emplean para el control de procesos en la producción y envasado de alimentos y medicamentos. Estos sensores garantizan la calidad y seguridad de los productos al asegurar la presión adecuada durante el proceso de fabricación.
- Industria del Petróleo y Gas: Los sensores de presión se utilizan en controles de pozos, monitoreo de presión de tuberías, medición de flujo y en el control de presión en reactores.
- Control de Procesos Industriales: Los sensores de presión son ampliamente utilizados en la automatización industrial para controlar y monitorear la presión en tanques, tuberías y sistemas neumáticos. También se utilizan en sistemas de aire acondicionado y refrigeración.
Estas son solo algunas de las muchas aplicaciones donde los sensores de presión desempeñan un papel fundamental. Su precisión y fiabilidad los convierten en dispositivos esenciales en una amplia variedad de industrias, garantizando el correcto funcionamiento de diferentes sistemas y procesos.
Qué características debes considerar al elegir un sensor de presión
Al elegir un sensor de presión, es importante considerar ciertas características que serán fundamentales para su correcto funcionamiento en tu proyecto o aplicación. A continuación, mencionaremos las características más importantes a tener en cuenta al seleccionar un sensor de presión:
Rango de medición
El rango de medición del sensor de presión indica el intervalo dentro del cual puede medir correctamente la presión. Es fundamental elegir un sensor cuyo rango de medición sea adecuado para tus necesidades específicas. Si necesitas medir presiones altas, asegúrate de que el sensor pueda soportar estas condiciones sin dañarse.
Precisión
La precisión del sensor de presión se refiere a la exactitud con la que puede medir la presión. Es importante considerar la precisión requerida para tu aplicación, ya que esto determinará qué tan confiables serán las lecturas del sensor. Si necesitas mediciones muy precisas, deberás buscar sensores con una alta precisión.
Tiempo de respuesta
El tiempo de respuesta es otro aspecto crucial al elegir un sensor de presión. Este parámetro indica cuánto tiempo tarda el sensor en responder ante los cambios de presión. Si necesitas mediciones rápidas y en tiempo real, deberás seleccionar un sensor con un tiempo de respuesta rápido.
Tipo de presión
Existen diferentes tipos de presión, como presión absoluta, presión relativa o diferencial. Es importante identificar qué tipo de presión deseas medir y seleccionar un sensor acorde a ello. Por ejemplo, si necesitas medir la diferencia de presión entre dos puntos, deberás optar por un sensor de presión diferencial.
Entorno de trabajo
El entorno de trabajo en el que se utilizará el sensor de presión también debe ser considerado. Algunos sensores son más adecuados para entornos industriales o agresivos, mientras que otros pueden utilizarse en aplicaciones más delicadas. Asegúrate de elegir un sensor que sea compatible con las condiciones ambientales y de trabajo a las que estará expuesto.
Calibración y compensación
La calibración y la capacidad de compensación del sensor son fundamentales para garantizar mediciones precisas y confiables. Verifica si el sensor cuenta con opciones de calibración y compensación, ya que podrían ser necesarias para ajustar las mediciones en ciertas condiciones o para corregir posibles errores.
Interfaz de salida
La elección de la interfaz de salida del sensor dependerá de cómo desees recibir los datos de presión. Puedes encontrar sensores de presión con salidas analógicas, digitales o incluso inalámbricas. Asegúrate de seleccionar una interfaz compatible con tu sistema o dispositivo de lectura de datos.
Al elegir un sensor de presión, debes considerar el rango de medición, la precisión, el tiempo de respuesta, el tipo de presión, el entorno de trabajo, la calibración y compensación, así como la interfaz de salida. Estas características son clave para asegurar un funcionamiento óptimo del sensor y obtener mediciones precisas de la presión en tu aplicación o proyecto.
Cómo se calibra un sensor de presión y por qué es importante
La calibración de un sensor de presión es un proceso esencial para garantizar su precisión y fiabilidad. Un sensor de presión descalibrado puede brindar mediciones incorrectas, lo que puede tener consecuencias graves en diversos sistemas y aplicaciones.
Existen diferentes métodos para calibrar un sensor de presión, pero en general, el proceso implica comparar las lecturas del sensor con un estándar confiable y realizar ajustes necesarios para asegurar que las mediciones sean exactas.
¿Por qué es importante calibrar un sensor de presión?
La calibración regular de los sensores de presión es fundamental por varias razones:
- Precisión: La calibración garantiza que las mediciones del sensor sean precisas y confiables, evitando errores en los resultados y mejorando la calidad de los datos obtenidos.
- Seguridad: En ciertas aplicaciones críticas, como en sistemas de control de procesos industriales o en aeronáutica, una medición inexacta de la presión puede tener consecuencias peligrosas. La calibración adecuada ayuda a prevenir situaciones riesgosas.
- Conformidad con estándares: Muchas industrias tienen regulaciones y normas que establecen requisitos específicos para la calibración de los sensores de presión utilizados en sus procesos. Cumplir con dichas normativas es fundamental para garantizar la aceptación y confiabilidad de los resultados obtenidos.
En general, se recomienda realizar la calibración de los sensores de presión con una frecuencia determinada por el fabricante o según las necesidades del sistema y la aplicación. Sin embargo, en algunos casos, factores externos pueden afectar el rendimiento del sensor y hacer necesario realizar calibraciones más frecuentes.
Aún cuando un sensor de presión se calibra, es importante seguir monitoreándolo para asegurarse de que continúe funcionando correctamente y brinde mediciones precisas a lo largo del tiempo. El deterioro gradual o las condiciones ambientales cambiantes pueden requerir ajustes adicionales o nuevas calibraciones periódicas.
Cuáles son los beneficios de utilizar sensores de presión en diversas industrias
Los sensores de presión son dispositivos fundamentales en muchas industrias, ya que permiten medir y monitorizar la presión de diferentes sistemas y procesos. Estos sensores ofrecen numerosos beneficios que mejoran la eficiencia y seguridad en distintas aplicaciones.
1. Control y automatización precisos
Gracias a los sensores de presión, es posible controlar y automatizar de manera precisa diversos procesos industriales. Estos dispositivos proporcionan información en tiempo real sobre la presión de un sistema, lo cual permite ajustarlo según las necesidades específicas y garantizar su funcionamiento óptimo.
2. Mejora de la calidad del producto
Al contar con sensores de presión, es posible monitorear y controlar la presión durante el proceso de fabricación de productos. Esto asegura que se mantenga una presión constante y adecuada, lo que resulta fundamental en sectores como la industria alimentaria, farmacéutica o automotriz, donde la calidad del producto es determinante.
3. Mantenimiento preventivo
Los sensores de presión también permiten implementar estrategias de mantenimiento preventivo en diversos equipos y sistemas. Gracias a que estos sensores pueden detectar y alertar sobre cambios en la presión, es posible tomar acciones correctivas antes de que ocurran averías o problemas más graves. Esto ayuda a reducir costos de reparación, tiempos de inactividad y mejorar la eficiencia operativa.
4. Seguridad y protección
En industrias como la petroquímica o la industria nuclear, donde el control de presión es esencial para evitar riesgos graves, los sensores de presión juegan un papel fundamental en la seguridad. Estos dispositivos permiten supervisar y controlar la presión en tiempo real, lo que ayuda a prevenir posibles fugas, explosiones u otros eventos peligrosos.
5. Optimización energética
Los sensores de presión también contribuyen a la optimización energética en diferentes procesos industriales. Al monitorear y ajustar la presión según las necesidades reales, es posible reducir el consumo de energía, disminuir los costos operativos y minimizar el impacto ambiental.
6. Integración con otros sistemas
Los sensores de presión pueden integrarse en sistemas de control de automatización más amplios, lo que permite una gestión más eficiente de todos los parámetros importantes. Esto facilita la supervisión y el control centralizado de diversos elementos en una planta industrial, mejorando la toma de decisiones y la eficiencia global.
Cuáles son las principales diferencias entre un sensor de presión absoluto y uno diferencial
Los sensores de presión se utilizan en una amplia variedad de aplicaciones para medir y monitorear la presión de un fluido. Dos tipos comunes de sensores de presión son los sensores de presión absoluta y los sensores de presión diferencial. Si bien ambos tipos cumplen la función de medir presión, existen diferencias fundamentales entre ellos.
Sensor de presión absoluta
Un sensor de presión absoluta mide la presión en relación a un punto de referencia absoluto, generalmente el vacío o la presión atmosférica estándar. Este tipo de sensor se utiliza cuando es necesario medir la presión real de un fluido sin considerar la presión ambiental.
El funcionamiento básico de un sensor de presión absoluta se basa en cambios en una propiedad física debido a la presión aplicada. Esto puede incluir cambios en la resistencia eléctrica, capacitancia o fuerza mecánica. El sensor convierte estos cambios en una señal eléctrica proporcional a la presión medida.
Uno de los beneficios de utilizar un sensor de presión absoluta es que proporciona mediciones precisas y confiables, ya que no está afectado por factores externos como cambios en la presión atmosférica. Esto lo hace adecuado para aplicaciones donde es crucial conocer la presión real del fluido.
Sensor de presión diferencial
Un sensor de presión diferencial mide la diferencia de presión entre dos puntos. Utiliza dos cámaras de presión separadas y mide la diferencia de presión entre ambas. Este tipo de sensor se utiliza cuando es necesario medir la presión en relación a un punto de referencia.
El principio de funcionamiento de un sensor de presión diferencial también se basa en cambios en una propiedad física debido a la presión aplicada. La diferencia de presión entre las dos cámaras del sensor se convierte en una señal eléctrica proporcional a esta diferencia. El valor de la señal resultante indica la diferencia de presión medida.
Una ventaja importante de utilizar un sensor de presión diferencial es que permite medir la presión relativa en lugar de la presión absoluta. Esto lo hace especialmente útil en aplicaciones donde es necesario comparar o monitorear la presión de dos puntos diferentes, como sistemas de ventilación, medición de flujo o sistemas de filtración.
Tanto los sensores de presión absoluta como los sensores de presión diferencial cumplen funciones importantes en diversas aplicaciones. La elección entre uno u otro dependerá de las necesidades específicas de cada caso particular.
Cómo se instalan y mantienen los sensores de presión correctamente
Para instalar y mantener correctamente los sensores de presión, es importante seguir algunas pautas y precauciones específicas. Estos pasos asegurarán un funcionamiento adecuado y una vida útil prolongada de los sensores:
1. Selección del sensor de presión adecuado
Antes de comenzar con la instalación, es fundamental seleccionar el sensor de presión apropiado para la aplicación en cuestión. La elección correcta dependerá de factores como el rango de presión requerido, el tipo de medio a medir y las condiciones ambientales. Es recomendable consultar las especificaciones técnicas del fabricante y realizar pruebas preliminares si es necesario.
2. Preparación del área de instalación
Antes de la instalación, se debe limpiar y preparar adecuadamente el área donde se colocará el sensor de presión. Asegúrese de que no haya obstrucciones ni suciedad que puedan afectar la precisión de las mediciones. Además, verifique que no haya fugas ni filtraciones en el sistema en el cual se trabajará.
3. Montaje del sensor de presión
Siga las instrucciones proporcionadas por el fabricante para montar el sensor de presión de manera correcta. Esto incluye utilizar los accesorios necesarios, como bridas o soportes, para fijarlo de forma segura en su lugar designado. Asegúrese de tener en cuenta cualquier consideración especial según la orientación requerida (horizontal o vertical) y garantice que el sensor esté nivelado y alineado correctamente.
4. Conexión eléctrica
Antes de conectar el sensor de presión a la fuente de alimentación o adquisición de datos, verifique que la tensión de operación sea compatible y respete las especificaciones del fabricante. Asegúrese de realizar una conexión adecuada y segura, siguiendo las indicaciones proporcionadas en el manual del sensor. Adicionalmente, se debe prestar especial atención al uso de cables blindados para minimizar cualquier interferencia electromagnética.
5. Calibración inicial
Una vez instalado el sensor de presión, es recomendable realizar una calibración inicial para verificar su precisión y ajustarlo si es necesario. Esto puede implicar el uso de un equipo de referencia y seguir los procedimientos específicos de calibración según las instrucciones del fabricante.
6. Mantenimiento periódico
Para mantener un rendimiento óptimo, es importante llevar a cabo un mantenimiento regular de los sensores de presión. Esto puede incluir inspecciones visuales para detectar posibles daños, limpieza cuando sea necesario y reajustes periódicos para asegurar mediciones confiables. Además, es fundamental revisar y cambiar los sellos y juntas si muestra signos de desgaste o fugas.
Siguiendo estos pasos durante la instalación y mantenimiento de los sensores de presión, se puede garantizar un funcionamiento correcto y confiable a lo largo del tiempo. Siempre siga las instrucciones proporcionadas por el fabricante y si tiene alguna duda o problema, consulte con un profesional capacitado.
Cuáles son las limitaciones y desafíos asociados con el uso de sensores de presión
Limitaciones de los sensores de presión
Si bien los sensores de presión ofrecen una manera eficaz de medir la presión en diversas aplicaciones, también presentan algunas limitaciones. Algunas de las principales limitaciones son:
- Rango de operación limitado: Los sensores de presión están diseñados para operar dentro de un rango específico de presiones. Si se excede este rango, es posible que el sensor no pueda proporcionar mediciones precisas o incluso puede dañarse.
- Sensibilidad a cambios de temperatura: Los sensores de presión pueden ser sensibles a los cambios de temperatura. Las variaciones en la temperatura ambiente pueden afectar la precisión de las mediciones y requerir calibración periódica.
- Imprecisión en bajas presiones: Algunos sensores de presión pueden tener dificultades para proporcionar mediciones precisas en rangos de presión muy bajos. Esto puede limitar su utilidad en aplicaciones que requieren una alta precisión en bajas presiones.
- Efecto de la posición: La posición del sensor de presión puede afectar sus mediciones. Por lo tanto, es importante colocar correctamente el sensor para obtener resultados precisos y confiables.
Desafíos asociados con el uso de sensores de presión
Además de las limitaciones mencionadas anteriormente, el uso de sensores de presión también puede presentar algunos desafíos. Estos desafíos incluyen:
- Interferencia electromagnética: La presencia de campos electromagnéticos puede afectar la precisión de las mediciones de los sensores de presión. Esto es especialmente cierto en entornos industriales donde se pueden encontrar fuentes de interferencia electromagnética como motores, equipos de soldadura, entre otros.
- Compensación de temperatura: Como se mencionó anteriormente, los cambios de temperatura pueden afectar la precisión de los sensores de presión. Para contrarrestar este efecto, a menudo se requiere una compensación de temperatura para obtener mediciones precisas en diferentes condiciones ambientales.
- Calibración periódica: Los sensores de presión generalmente requieren calibración periódica para garantizar mediciones precisas a lo largo del tiempo. La falta de calibración puede resultar en mediciones incorrectas y afectar el rendimiento de las aplicaciones en las que se utilizan.
- Durabilidad: Dependiendo del entorno de uso, los sensores de presión pueden estar expuestos a condiciones adversas como vibraciones, golpes o ambientes corrosivos. Estos factores pueden reducir la vida útil del sensor y requerir reemplazos frecuentes.
A pesar de estas limitaciones y desafíos, los sensores de presión siguen siendo una herramienta invaluable en una amplia gama de aplicaciones, desde la industria automotriz hasta la monitorización médica. Con un uso adecuado y considerando sus limitaciones, los sensores de presión nos permiten obtener mediciones precisas y confiables para satisfacer nuestras necesidades.
Qué avances tecnológicos se han realizado en el campo de los sensores de presión en los últimos años
En los últimos años, se han realizado avances significativos en el campo de los sensores de presión, lo que ha llevado a mejoras en la precisión y la capacidad de medición. Estos avances han permitido la creación de sensores más pequeños y eficientes, así como también la integración de características adicionales.
Uno de los principales avances ha sido el desarrollo de sensores de presión de película delgada. Estos sensores utilizan una película sensible a la presión que se coloca sobre un sustrato de vidrio o silicio. Esta tecnología permite la fabricación de sensores muy pequeños y livianos, lo que los hace ideales para dispositivos portátiles y aplicaciones médicas.
Otro avance importante ha sido la implementación de la tecnología MEMS (Micro Electro-Mechanical Systems) en los sensores de presión. Esta tecnología combina componentes mecánicos y electrónicos en un mismo dispositivo y ha permitido la creación de sensores más precisos y confiables. Los sensores MEMS de presión también son más resistentes a las perturbaciones ambientales, como la vibración y la temperatura, lo que los hace adecuados para aplicaciones en entornos difíciles.
Además, se han desarrollado sensores de presión inteligentes que cuentan con capacidades adicionales, como la compensación de temperatura y la capacidad de autocalibración. Estos sensores son capaces de ajustar automáticamente sus mediciones en función de las condiciones ambientales, lo que mejora la precisión y la estabilidad a largo plazo.
Los avances tecnológicos en los sensores de presión han permitido la creación de dispositivos más pequeños, precisos y confiables. Estos avances han ampliado las posibilidades de aplicación de los sensores de presión en una variedad de industrias, desde la automotriz hasta la medicina. Con el continuo desarrollo de nuevas tecnologías, es probable que veamos aún más mejoras en los sensores de presión en el futuro.
Espero que estos temas te sean útiles para escribir tu artículo. ¡Buena suerte!
Sensores de presión: ¿qué son y cómo funcionan?
Los sensores de presión son dispositivos que se utilizan para medir la presión de un fluido o gas en un sistema. Estos sensores convierten la presión en una señal eléctrica que puede ser interpretada por otros componentes, como una computadora o un microcontrolador.
Existen diferentes tipos de sensores de presión, pero en general, todos funcionan de la misma manera. La presión ejercida sobre el sensor causa una deformación mecánica en su estructura, que a su vez produce un cambio en alguna propiedad eléctrica del sensor, como la resistencia o la capacitancia. Este cambio es detectado por el sensor y convertido en una señal eléctrica.
En términos básicos, el proceso de funcionamiento de un sensor de presión se puede resumir en los siguientes pasos:
- El fluido o gas ejerce presión sobre el sensor.
- La presión causa una deformación mecánica en el sensor.
- La deformación mecánica produce un cambio en alguna propiedad eléctrica del sensor.
- El cambio en la propiedad eléctrica es detectado y convertido en una señal eléctrica.
Esta señal eléctrica puede ser analógica o digital, dependiendo del tipo de sensor. Los sensores de presión analógicos producen una señal eléctrica proporcional a la presión medida, mientras que los sensores de presión digital generan una señal binaria que representa la presencia o ausencia de presión.
Tipos de sensores de presión
Existen varios tipos de sensores de presión, cada uno con sus propias características y aplicaciones específicas. Algunos de los más comunes son:
- Sensores de presión piezorresistivos: estos sensores utilizan una resistencia sensible a la presión para medir cambios en la presión.
- Sensores capacitivos: estos sensores miden la presión a través de cambios en la capacidad eléctrica de un condensador.
- Sensores de membrana: estos sensores incorporan una membrana delgada que se deforma bajo presión, produciendo un cambio en una propiedad eléctrica.
- Sensores de presión diferencial: estos sensores miden la diferencia de presión entre dos puntos para determinar la presión absoluta.
Cada tipo de sensor tiene sus ventajas y desventajas, por lo que es importante elegir el sensor adecuado para cada aplicación específica. Algunos factores a tener en cuenta al seleccionar un sensor de presión incluyen la precisión requerida, el rango de presión a medir, la temperatura de trabajo y el entorno en el que se utilizará.
Los sensores de presión son dispositivos importantes en diversos campos, desde la industria automotriz hasta la medicina. Su funcionamiento se basa en la conversión de la presión en una señal eléctrica, que luego puede ser interpretada por otros componentes electrónicos.
Un sensor de presión es un dispositivo que mide la presión de un fluido o gas y la convierte en una señal eléctrica.
Un sensor de presión utiliza diferentes tecnologías, como el uso de membranas o piezoresistores, para medir los cambios en la presión y convertirlos en una señal eléctrica.
Los sensores de presión se utilizan en una amplia variedad de aplicaciones, como la monitorización de procesos industriales, control de la presión en neumáticos, sistemas de climatización, entre otros.
Algunos de los tipos de sensores de presión más comunes son los sensores de presión capacitivos, piezorresistivos, ultrasónicos y de tipo bourdon. Cada uno tiene sus propias características y aplicaciones específicas.
La sensibilidad se refiere a la capacidad de un sensor para detectar pequeños cambios en la presión y convertirlos en una señal eléctrica. La precisión se refiere a qué tan cerca está la lectura del sensor del valor real de la presión medida.
Deja una respuesta
Entradas relacionadas